Salt Lake City Water Damage Restoration is an intricate process that requires specialized equipment and expertise. Professionals take a systematic approach to getting all the water out, drying the area and sanitizing it.
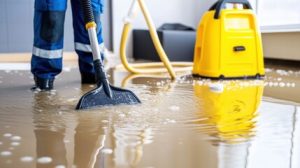
The first step is an initial assessment of the water damage. Professionals inspect the area using tools like moisture meters and thermal imaging cameras.
One of the most important parts of water damage restoration is assessing the extent of the damage and how it can be repaired. This step involves a thorough inspection by a trained professional who will use a variety of equipment to assess the situation, including moisture detectors and thermometers.
Once the professional has assessed the level of the water damage, he or she will begin the cleanup process by identifying and blocking off any unsafe areas and stopping the flow of additional water into vulnerable spaces. Depending on the severity of the damage, this may involve turning off valves, shutting down water supplies or even using pumps to divert water from problem areas. The goal is to get as much water out of the area as possible, as the longer it stays there, the more extensive and costly the damage will be.
In addition to preventing structural damage, prompt water damage restoration can also help to prevent mold growth and other health problems. The fungus thrives in damp, dark environments and can cause serious illness in occupants of affected buildings. A thorough water damage restoration process includes sanitizing and drying the area to eliminate mold spores and other pathogens.
When left untreated, water damage can lead to the deterioration of building materials and the collapse of certain structural elements. Prompt action can prevent such problems and save lives and reduce economic losses.
A comprehensive water damage assessment program should include a set of local, defined standards for initial assessment and detailed damage assessment. These should be clearly written and in accordance with any higher-level guidelines and state requirements. They should also take into account the unique environment of the facility, such as a manufacturing operation, medical office or storage warehouse.
Removing the Water
Water damage restoration is a complex process that involves several stages. The first step is to assess the damage and determine the scope of work that needs to be done. This step includes checking for safety hazards and structural damage such as sagging walls or floors. It also includes identifying the source of the water and taking steps to prevent future problems.
The next step is to remove the water from the affected area. This can be done by using a wet/dry vacuum or pumps for deeper water accumulations. It is important to remove as much water as possible because the longer it stays in place, the more damage it will cause. This damage can include damage to drywall, flooring, furniture, and appliances. It can also lead to mold and mildew growth, which can be harmful to your family’s health.
Once the water is removed, the area must be dried out. This is important because it can prevent further damage to your property and prevent the formation of mold and mildew. It can also help protect your home’s structure and minimize the cost of repairs. The drying process may take a few days or weeks, depending on the severity of the water damage.
It is important to contact a professional company for water damage restoration. They will be able to help you restore your property quickly and efficiently. They will also be able to assist you with filing an insurance claim. When you file an insurance claim, it is important to save receipts for any additional living expenses that you may incur as a result of the damage. Additionally, it is helpful to have photos of the damage before and after the water damage repair process begins.
Drying the Area
Drying the area is a critical part of water damage restoration. This step removes excess moisture from building materials and helps mitigate issues with air quality and structural integrity that may result from prolonged water exposure. It also prevents the growth of mold and other harmful microorganisms.
During the drying process, professionals use fans and dehumidifiers to circulate warm, dry air throughout the affected area. Then they use specialized equipment to measure the moisture level in the affected materials and adjust the equipment as necessary. This ensures that all of the moisture is removed, which can prevent future problems like mold growth and structural deterioration.
Moisture is the perfect breeding ground for mold spores, which can grow within 24 to 48 hours of water exposure. Lingering moisture can cause drywall and wood to warp and swell, resulting in costly structural repairs. And if the spores get into your lungs, they can lead to respiratory problems.
The best way to avoid this is to make sure the area dries quickly and thoroughly after water removal. This involves assessing the extent of the damage, protecting valuables, and ensuring that all of the moisture is removed. It also requires determining what can be repaired, such as refinishing a wooden floor or replacing wallpaper and carpets.
If you’re experiencing significant water damage, it’s important to consult with a professional right away. They have the equipment and experience to handle the cleanup quickly, efficiently, and safely. They can also help you locate the source of the water damage, turn off power, and take other steps to protect your property and keep you and your family safe. And once the flood waters recede, they can restore your home and get it back to normal as quickly as possible.
Sanitizing the Area
When water damage occurs, it can affect not only the structure of your property but also the materials and furnishings inside. This is why it’s important to hire a company that specializes in water damage restoration. These professionals can assess the severity of the damage and use the proper equipment to dry, clean, and sanitize the affected areas.
They can also repair structural damages, including drywall and flooring. If necessary, they can even reconstruct sections of your home or office to return them to their pre-damage state. They will also use environmentally friendly cleaning and drying methods to minimize the impact on your health, safety, and the environment.
First, they’ll find the source of the leak and shut off any water supplies. They may also use pumps to remove excess water and help prevent additional damage. They’ll also remove any damaged items that can’t be salvaged, including carpet padding, drywall, and insulation. This can speed up the drying process and prevent further damage to the property.
Finally, they’ll sanitize the area by using disinfectants and a deodorizer. This will prevent further damage, including mold growth, which can occur in moist environments. Mold spores can trigger allergies and other health problems in some people, so it’s essential to get them cleaned up as quickly as possible.
Water damage restoration is a vital service for homeowners and businesses alike. It can restore the appearance and functionality of a property after flooding or prolonged leaks. It can also protect property values and save on costly repairs down the road. The key to successful water damage restoration is quick action, so it’s important to call in the experts as soon as you notice any signs of trouble.
Restoring Your Property
The restoration process is a comprehensive, professional effort to return the property to its pre-loss condition. This typically involves mitigating water damage, drying structures with specialized equipment, cleaning and sanitizing the affected areas, and completing structural repairs. It also includes taking steps to prevent future problems, such as mold growth and deterioration of building materials.
The longer a water damage event goes unaddressed, the more extensive and expensive it becomes to repair. Secondary damage can include mold growth, rotting of building materials, and a decrease in home value. In addition, a lack of timely repairs can lead to higher homeowners’ insurance rates in the future.
Water damage can damage valuable possessions, including electronics and furniture. It can also contaminate items that hold sentimental value, such as family photos or personal papers. The best way to increase the odds of salvaging these items is to contact a water damage restoration expert promptly. The sooner the water is removed, the less likely it is that these items will be permanently lost.
In addition to removing standing water, restoration professionals use moisture detectors and hygrometers to evaluate the extent of the damage. They also dry the affected areas using industrial-grade dehumidifiers and air movers. They may also clean and sanitize the area to remove bacteria, germs, and other contaminants.
A thorough inspection and assessment by a water damage restoration expert can help you save money in the long run. It can also reduce the risk of mold growth and deterioration of building components, which can lower the value of your home and cause ongoing maintenance costs. Moreover, taking preventive measures like waterproofing your basement and improving drainage can reduce the risk of future water damage.